I really enjoyed painting the wings. The Stewarts Paint System is fantastic! You just have to remember to etch the aluminum before priming and painting. I painted some smaller AL parts and forgot to etch. The paint does not stick as well.
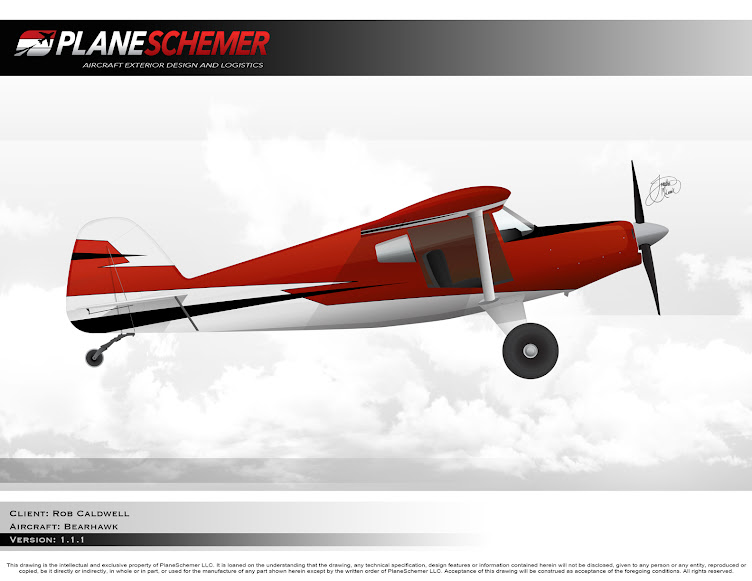
Welcome to a Builders Blog of my Bearhawk 4 Place.
Build date started: June 1, 2018.
❗️Scroll to the bottom to start at the beginning of the build❗️
Click HERE to return to the beginning of this Bearhawk Builder blog.
Wednesday, December 23, 2020
Saturday, October 31, 2020
Installing the Hoerner Wing Tips
These carbon fiber Hoerner style wing tips increase the total wing span to over 36 feet! The tips are 18" each, so I decided to install a rib for rigidity to each.
Tuesday, September 29, 2020
Wing Assembly
The Bearhawk (Model B Ribblet Airfoil) is pre-assemled at the factory. My job is to install the fuel tanks, ailerons, flaps, rigging, wing tips... Prime and Paint! It took me almost 3 months to assemble and paint both wings.
Monday, September 14, 2020
Moving Day
The day has finally arrived! We are moving the fuselage to the Statesville airport where it will stay until I have completed assembling and painting the wings.
Saturday, September 12, 2020
Wednesday, August 26, 2020
Airbox - Multiple Iterations
I originally wanted a conical airbox from James Aircraft to sit in front of the Fuel Servo. I just could not get it to fit. So after multiple attempts, I ended up casting a square fiberglass box for a rectangular K&N filter. That also had some fitment issues, so I reluctantly modified the bottom of the cowling with a fiberglass blister to accommodate the final version. With this increased filtered surface area should give better flow, and maybe a little more HP?
Monday, August 3, 2020
Gull Wing Doors with Carbon Fiber Frames
I really wanted a light weight CF door covered in Lexan. I got what I wanted, but I'm not sure I would do it again. It was quite a job fabricating the CF door frames. I lined them with Kevlar to prevent galvanic corrosion and aluminum backers where there will be rivets. The handle came from Hendrick Manufacturing and are typically used on RV's.
Friday, July 24, 2020
Thursday, July 16, 2020
Installing the Windscreen / Windscreen Fairing (Challenges)
Whoops! I trimmed the windscreen too short!
The Bearhawk 4 Place uses the Cessna 170 windscreen. Only slight trimming is need to fit the windscreen to the boot cowl. My trimming was not slight. The fix is to enlarge the windscreen fairing and fabricate a piece coving piece for the inside of the windscreen.
These pictures tell the story...
Fuel Lines ~ Firewall Forward
The firewall forward installation of the fuel lines was very straight forward. No issues. I optimized the routing by securing the lines to the engine case/sump with cushioned high temp adele clamps.
Routing from the firewall goes like this:
- Port side lower bulkhead fitting to mechanical (engine driven) fuel pump
- Mechanical fuel pump to forward facing fuel controller
- Fuel controller (metered fuel) to fuel flow transducer (top of the engine case)
- Fuel flow transducer to fuel flow divider (spider)
The fuel lines I selected are not the typical fire sleeved lines from most aviation supply houses. These lines are from TS Flightlines. Tom Swearingen is the owner and takes great care in consulting with the home builder before assembling the lines. Tom has purposely designed a better fuel line that is braided in stainless steel and covered (integrated) with teflon. Just one example of why his lines are superior... Standard lines are rated to 1,000psi. TS FLightlines are rated to 3,000psi.
SPECS....
NEW Integrated Teflon Firesleeve
|
Standard Teflon Firesleeve
(Stratoflex 101)
| |
Conductive Teflon Liner
|
.030 Wall
|
.020 Wall
|
304 Stainless Braid
|
.006 Wire
|
.002 Wire
|
Working Pressure
|
3000 PSI
|
1000 PSI
|
Temperature Rating
|
-76*/+500*
|
-65*/+450*
|
High Temp Silicone Outer Cover
|
*.060 - .090 Thick
|
AS1072 Firesleeve
|
SPECS:
Wednesday, July 15, 2020
Installing the Hartzell Trailblazer 84" Propeller
I am using the Hartzell 83" Trailblazer composite propellor. This was tested by Mark Goldberg of the Bearhawk factory (AviPro Aircraft). Everyone I spoke that has flown behind this prop LOVES it! Very lightweight and exceptional performance.
Hanging the prop is fairly straight forward. Hartzell technical service department was very helpful. I confirmed a few things with them from the manual. Prop governor installation and set up, prop hub orientation, safety wiring, etc. The manual tightening the prop hub to 40 ft lbs each bolt. There is a bolting sequence to be followed. You can't do it without a propellor wrench. Hartzell sells propellor wrenches, but the Ultimate Propellor Wrench works best! https://antisplataero.com/products/ultimate-propeller-wrench
Sunday, July 5, 2020
Monday, June 22, 2020
New Fairlead for Rear Seat Bracket
You can see in this picture after installing the rear seat, the left rudder cable rubs against the left rear seat bracket. These pics demonstrate the fix.
Tuesday, May 19, 2020
Ignition System - The Magneto vs. Electronic Ignition Decision
Saturday, March 14, 2020
Drilling the Wings to the Fuselage
Friday, January 17, 2020
Wiring and Electrical System
Ok, the Electrical and Wiring process went very well! But I could not have done it without the help of Jason Smith at Aerotronics. Aerotronics built my instrument panel and then shipped it to me. After I mounted the panel and it was my job to bring all of the wires (fuel pump, lights, sensors, battery contactor, P-Leads, etc) through the firewall to panel. This is accomplished with a 37 pin P1 Circular Connector Plug, a.k.a., the P1 Plug. Aerotronics prewires the female end of the P1 Plug at the panel. They map all of the pin locations and then send me the pin map for wiring the male end of the P1 Plug that I assemble. In addition, based on my choice for a ignition system, Aerotronics also supplied me with a schematic for everything else to be brought through the firewall going to the circuit breaker panel. It's a full diagram of the entire wiring system firewall forward. I couldn't have done it without their help. I read Bob Knuckles book, The Aeroelectric Connection as well as other related books and websites to help me understand the process, methods and technical aspects.